2017
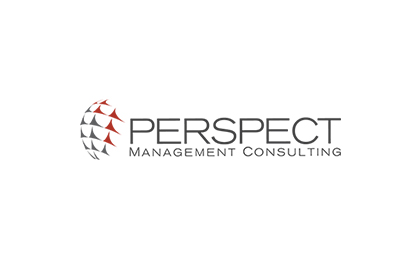
Lean – Another Tool?
Posted by Perspect
WHAT IS LEAN?
There has been significant discussion as to what lean is and what it is not as of late. Lean is,
a way of doing business. It is not, an initiative, a tool or a cost cutting spiral; it enables fulfillment of public service promises through the delivery of the right services at the right time in the most efficient means continuously
a way of doing business. It is not, an initiative, a tool or a cost cutting spiral; it enables fulfillment of public service promises through the delivery of the right services at the right time in the most efficient means continuously. Lean is a business philosophy. To be truly successful, all employees¹ must adopt lean at an organizational level over time. Lean thinking is, or should be based on three main principles
- Removing overburden – make life easier for employeesand respecting people;
- Waste removal – where waste is defined by the customer not the organization;
- Leveling activity – reducing peaks and troughs of activity
Too often organizations begin by trying to remove waste through the adoption of a select few tools in complete isolation of the needs of the customer, the strategic need for change and the needs of the employee. The result often is minimal delivery of value to the customer, a misalignment to organizational strategy and failure to engage employees. In fact, the approach of focusing only on waste removal can be alienating to employees and as such starting with the facet of removing overburden can result in a much more sustainable approach to the development of a cultural of continuous improvement and engagement.
A better place to start may be to ask employees what is not working well in their jobs today and follow up with root cause analysis exercises to really understand where the challenges lie.
A better place to start may be to ask employees what is not working well in their jobs today and follow up with root cause analysis exercises to really understand where the challenges lie. This will result in a connection between operations and strategy; between staff and management.
Studies have shown that adoption of waste removal only, can result in:²
- Poor sustainability, especially of a kaizen blitz approach;
- Technology, tools and techniques (TTT) used without understanding of customer needs;
- TTT used without understanding business needs;
- TTT thrown at business problems, often in wrong order;
- People don’t understand the quality side of lean;
- Used only at the floor level leaving management disengaged.
The result is a lot of wasted opportunity as people become fixated on tools without realizing that these are just tools. They are only a means to an end.
A lean organization understands respect for people, stakeholder value and focuses its key processes to continuously improve it.
A lean organization understands respect for people, stakeholder value and focuses its key processes to continuously improve it. The ultimate goal is to provide perfect value to all stakeholders through a perfect value creation process that has zero waste.
How does lean work?
If applied effectively in its entirety, lean thinking becomes a way of life for an organization, changing the focus of management from optimizing separate technologies, assets and departments to optimizing the flow of services through entire value streams that flow horizontally across departmentsto stakeholder
lean thinking becomes a way of life for an organization, changing the focus of management from optimizing separate technologies, assets and departments to optimizing the flow of services through entire value streams that flow horizontally across departments to stakeholder
(including customers). Silos in organizations contribute on average for up to 30% of inefficiencies, lean addresses this.
Eliminating waste along entire value streams, instead of at isolated points, creates processes that generally need less human effort, capital and time to deliver higher-quality services compared to traditional business systems. Organizations are able to respond to changing customer desires with increased variety and quality while decreasing response times and costs. Also, information management becomes much simpler and more accurate, allowing for the transparency and accountability demanded in the public sector.³
With this being said, lean does not preclude more resource intensive and complex processes from the value delivery system when they distribute greater value to the stakeholder body as a whole with less waste.
The context of value should be in terms of outcomes, not in the activity from which they were derived or the entity which created it.
The context of value should be in terms of outcomes, not in the activity from which they were derived or the entity which created it.
As highlighted above, it is common for organizations embarking on a lean journey to begin with the building blocks such as VSM and Kaizens, and then to move towards more advanced tools such as strategic deployment also referred to by some as Hoshin Kanri. Sometimes the lean changes are planned from the beginning, whereas in other instances these changes are in reaction to a realization that point-in-time improvements, while yielding fantastic outcomes, in and of themselves are not strategic in nature, and do not create a sustainable solutions to the challenges faced by the organization nor do they result in a culture aligned to the vision of the organization.
Keys to successful organizational change include the ability to articulate the sense of urgency, the inspiration and the need for change. This communication strategy creates the necessary awareness within the organization to enable the change. As such an integrated approach to individual and organizational change as well as program delivery must be implemented in transformational exercises.
What does cultural transformation look like?
In order to achieve the breakthrough strategies required to address key business issues, cultural transformation is often necessary.
Strategic deployment will facilitate a paradigm shift towards a culture of continuous improvement and engagement.
Strategic deployment will facilitate a paradigm shift towards a culture of continuous improvement and engagement. Employees want to be utilized in more productive roles and to feel that they contribute to the organization in a more positive way. Employee engagement is crucial to the realization of more customer-centric services and efficient processes as it is the employees who understand what the customer wants and how existing processes work. Employees must be part of the solution development. This is one of the fundamental differences between traditional strategic planning and execution and strategic deployment. Strategic deployment leverages a top-to-bottom and bottom-to-top cascading approach to planning and implementation, which engages every employee in a meaningful manner in planning the organization’s strategy, objectives and tactics.
The development of an engaged culture of continuous improvement, which encourages people at all levels of the organization to identify, simplify and streamline the services that the customer needs, is how organizations will succeed in addressing key business challenges. Employees will take pride in their work, knowing that they are making a difference to their customers because they are designing and delivering programs and services that people need and want.
By adopting continuous improvement as a way of doing business, not as a one-time project and not as a fad, the pursuit of perfection becomes the goal that drives performance to leading levels.
Working through people who work on continuous improvement is the key to this principle.
Working through people who work on continuous improvement is the key to this principle. It cannot be applied by doing it to people.
Organizations can not continue doing business the same way and expect different outcomes.
Contact
Colin McAllister
Perspect Management Consulting Inc.
101-8143 Fairways West Drive,
Regina, SK S4Y 1A9
Office: 306-543-2231
Mobile: 306-591-5101
Email: colin@perspect.ca